RC Baja BUGATTI Type 57

Construction
The construction of the project has gone well, all parts slated for each manufacturing check-in were all started and completed on time. The majority of the parts were 3D printed with most of the parts needing to be more resilient being printed out of a Nylon Carbon Fiber and all remaining parts were printed with ABS or PLA. The chassis was cut out by being held to the end of a workbench with a custom jig and cut with a circular saw with enough material on the part to cut out a spare chassis in case of emergency. As of Spring quarter, the vehicle had gone through some cosmetic changes as well as replacing some parts that have failed through testing, all components were functioning in time for the competition.

Figure 1 shows the parts printed by the end of period 3 for the manufacturing check-in. Top left is an image of the motor mount with all mounting holes to attach the motor to the mount and mount to the chassis and have space for the reduction gears and axles to operate. Bottom left is the reduction axle mount, the partner piece has already been printed, both pieces on the left are made of the nylon carbon fiber. Top right is the battery housing the secure the battery to the chassis. Bottom right is the gearbox housing to keep any unwanted material from entering the gear and differential system; both parts on the right side were printed out of ABS.
Figure 1 - 1/3 of manufactured parts

Figure 2 shows the metal lathe that the axles for the RC car will be manufactured on. The machine works by spinning the Aluminum at high speeds and using hardened carbide steel bits to cut the aluminum to the desired diameter and length. As a trained and experienced manufacturer on the metal lathe, there are no unforeseen issues expected in the use of this machine.
Figure 2 - Metal Lathe

Figure 3 shows the the Plasma CNC Machine that may be used on a lower operating level to cut through the aircraft aluminum for the chassis. The machine works in the same sense that water jet cutters work by forcing a reaction through a piece of material but the plasma cutter sends an electric arc if either shop air, nitrogen, argon, oxygen or other noble gas to cut through the material. The plasma cutter shows potential to not cut through the Aluminum from complications with the metal and has a higher chance of working properly through steel, not being trained on this instrument a technician will need to assist in the manufacturing process.
Figure 3 - Plasma CNC Machine
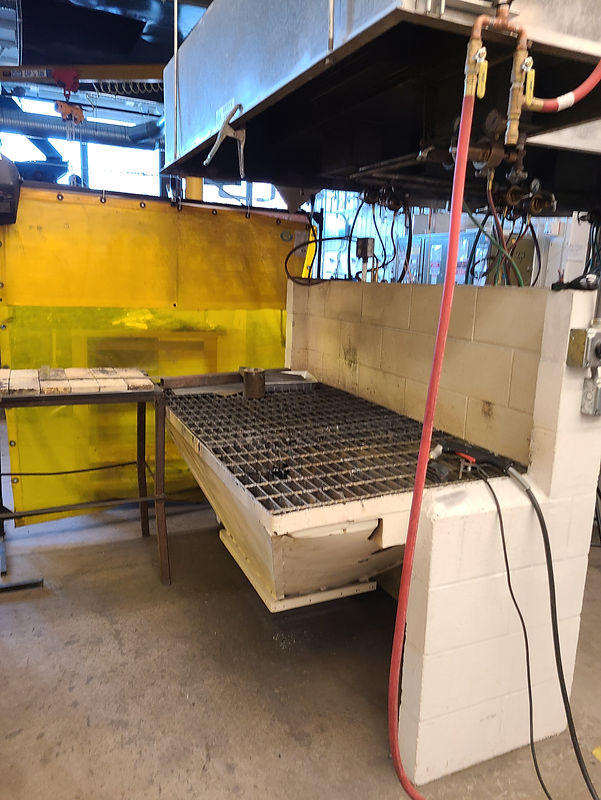
Figure 4 shows the handheld version of the plasma cutter and operates in the same way but is a manual adaptation to the autonomous CNC version. This version may also be used to cut the Aluminum as to control the firing mechanism during the process to avoid any operational issues that arise from operating the plasma cutter with the improper tip to cut the Aluminum. Again, not being trained on this machine, a technician or other trained faculty member will need to assist in this tool's operation.
Figure 4 - Handheld plasma cutter
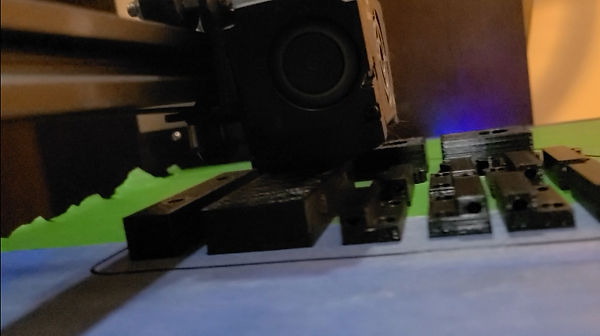
Figure 5 shows a group of parts slated for reprinting to replace altered parts. Parts include control arm mounts, reduction axle mounts, differential mounts, wheel to bearing adapters and a finalized gear to be cast and mounted to the motor. With the completion of one other print beyond this all parts will be done and the car will become assembled for the week 10 functioning vehicle check-in.
Figure 5 - Ender 3-Max 3D printer
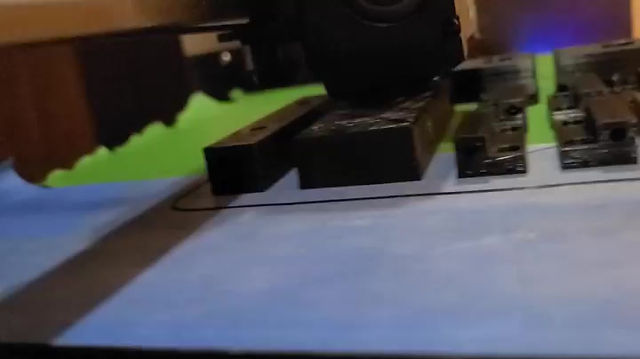
Video 1 shows the construction of various vehicle parts being constructed out of PLA to the specific size and shape necessary to accommodate the needs of the project. The majority of the parts of the vehicle were printed using PLA printed from team member Alex Vornbrock's personal printer or printed out of a Nylon Carbon Fiber filament out of the MakerBot 3D printers located in Hogue Hall of CWU. This process has proved very useful in the creation of custom parts for a variety of projects.
Video 1 - 3D printed Construction

Contact
I'm always looking for new and exciting opportunities. Let's connect.
123-456-7890