RC Baja BUGATTI Type 57
Schedule
The three major portions of this project (Design, Construction, and Testing) will be broken up into the three remaining quarters for senior year; design in the fall, construction during winter and testing through the spring. The design phase will take place during the Fall quarter (effective dates are 09/21 - 12/6/2022) and is represented in the Gantt chart below; students will take design concepts for their individual projects while following up with analyses that prove why the designs are acceptable parameters for the project. Through the duration of Fall quarter students will have created a senior project proposal in accordance with Central Washington University Engineering Department guidelines, including the completion of the introduction section of the proposal (Section 1 with a minimum of 20 requirements the vehicle must meet), the design and analysis section (Section 2 with a minimum of 12 analyses of the project in question), as well as the remaining written sections of the proposal (Sections 3-9): the Methods and Construction, Testing, Budget, Schedule, Project Management, Discussion and Conclusion of the project.
The construction of the vehicle will take place during winter quarter (effective 01/04 - 03/10/2023) with a focus on defining the testing parameters and budget for the scope of the project; in this time teams will have also purchased, obtained, created, crafted and assembled all parts and systems integral to the operation and success of the project. The final section of the project will take place during the Spring quarter, focusing on the testing portion of the project as to ensure the projects are meeting requirements and are operating to standards set by the RC-Baja Competition Rules as well as the requirements set by the individual student described within their individual proposal. The schedule will continue to be updated as the project progresses in accordance to making necessary changes to accommodate unforeseen scheduling conflicts and delays.
During the construction phase through winter quarter team members held focus on printing the pieces on the 3D printers or cutting the aluminum on the CNC machine. Minor adjustments and general sanding and fitting were done with most all parts as some were made to be a tight fit. Once sufficient parts were made the remaining purchased parts were obtained as to get the assembly of the vehicle underway to begin the testing phase in Spring quarter. The manufacturing check-in during winter quarter period 5 was completed on time with the various parts either printed out of PLA, ABS or Nylon Carbon Fiber filaments, being cut on the handheld plasma cutter, or cut out of Aluminum on a metal lathe. All parts are expected to be finished in time for the period 8 manufacture check-in and teams will begin the assembly of the vehicle.
Spring quarter focused on the testing of the vehicle; this team member held a focus on testing the drivetrain and chassis. The first test concentrated on the motor efficiency to ensure the motor will not overheat during the competition given a maximum of five minutes during each test; the test reduced the downtime between each trial to only three minutes to ensure the motor was under ample stress. The second test made use of the INSTROM machine in Hogue 127 to test the deflection of the chassis under various loadings. The final test focused on the maximum speed test to ensure the car would meet the required speed set in Fall quarter and that the vehicle will perform well during the competition.
Current Project Schedule: Gantt Chart (05/26/23)

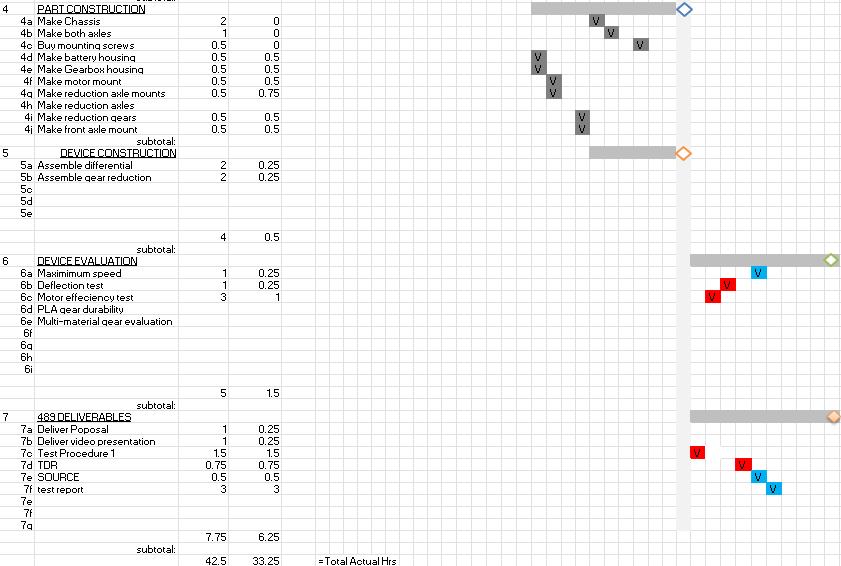